Let's Pioneer The Future Together
Let Me Show You Some Cases- Manufacturer Audits For North America
The client is a wood processing machinery manufacturer located in Canada.
The customer requires Inertia China to complete an audit of its designated machinery manufacturer.
In addition to following the professional audit process and standards, Inertia China also obtains some industry-specific and special requirements and priorities from our customers.
Inertia China visits manufacturers, completes complete factory visits, audits, and meets with supplier management teams and employees to obtain authentic and timely information and evidence during audits.
All content, feelings and recommendations of the audit are shared with the client, and all findings and observations are summarized into an audit report.
This cooperation gives customers greater confidence that their manufacturers in China will be able to continue to support their production and quality needs, and to better understand the business potential of their suppliers.

How We Proceed Factory Audit?
Step 1 - Preparation | Step 2 - Full On-Site Audit | Step 3 - Report |
Review & Communicate
Customer Requirements Internal Meeting & Schedule |
Check With ISO9001 & 13485
Open & Transparent Communication |
Specialization, Logic
Seek Truth From Facts Real-World Tailored Solutions |
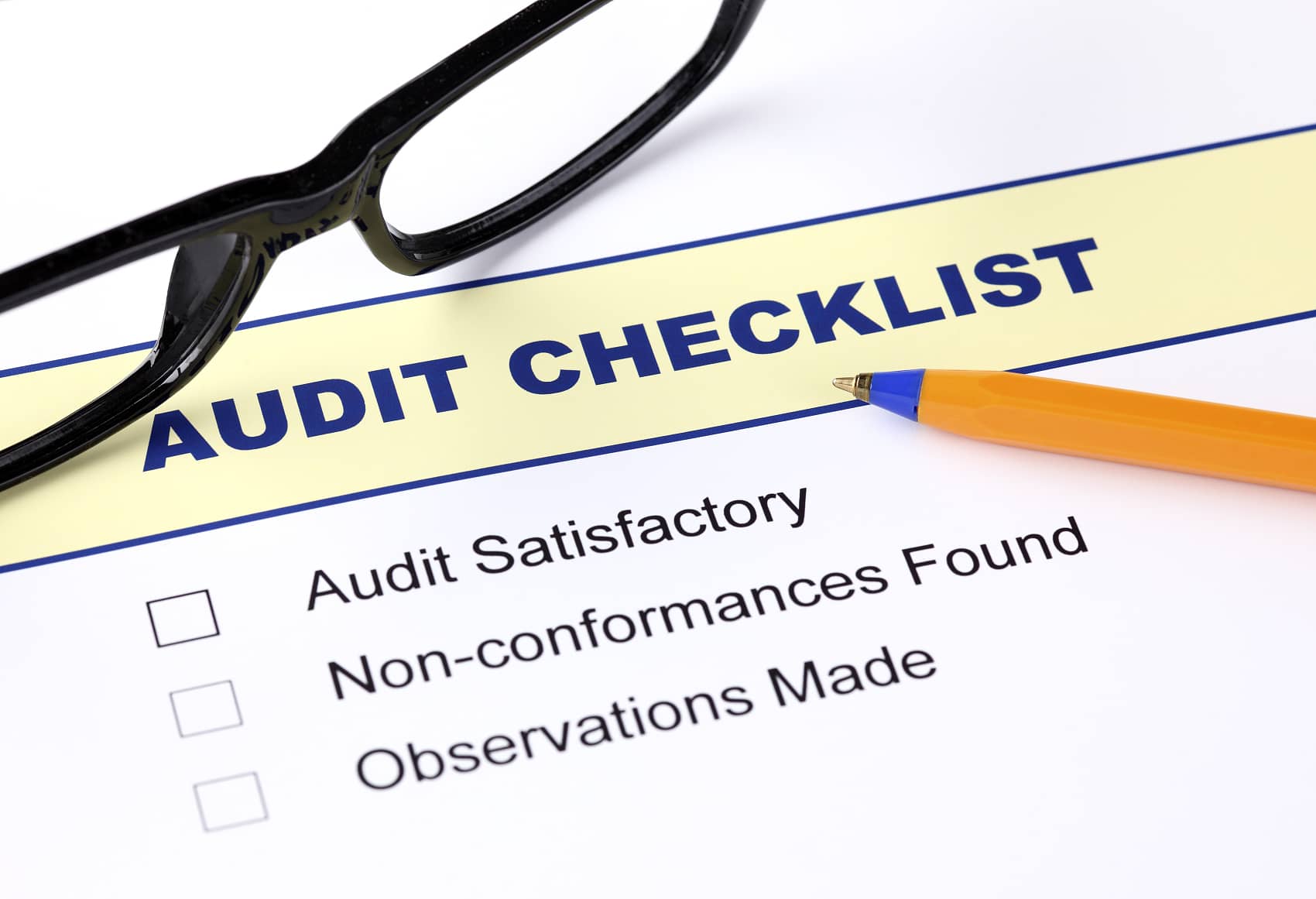
What We Found
- Work Instructions should be posted on site.
- Equipment inspection list and maintenance records should be on site.
- Product status areas should be planned on site.
- The site should be kept clean (processing dust in time).
- On-site inspection equipment should be checked in time.
- The finished product to be inspected shall be marked with the corresponding status.
- The nonconforming products on site shall be marked accordingly.
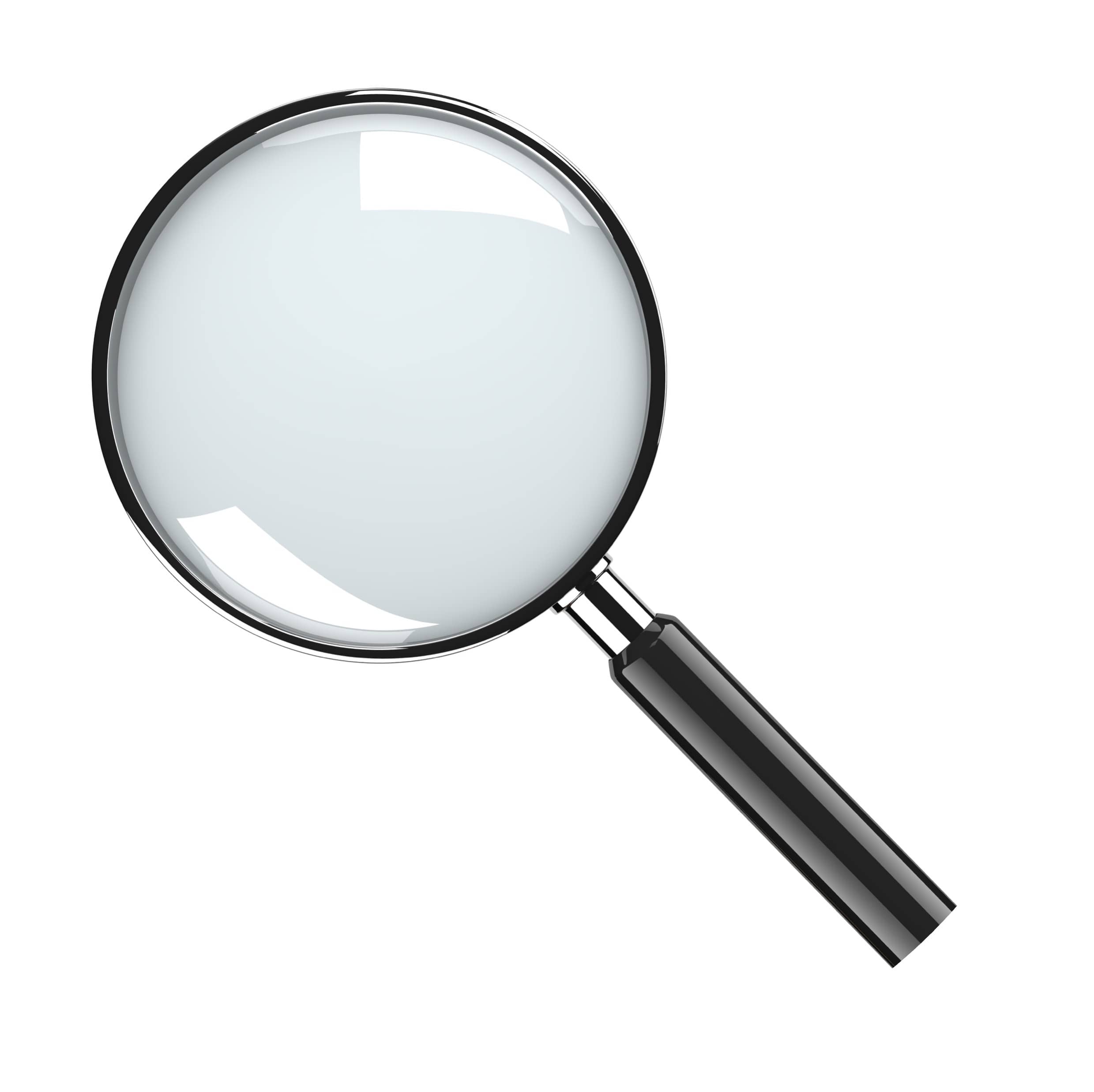
Let Me Show You Some Cases- Quality Management for a kind of Chiller
- The customer relinquishes authority over the product's quality level.
- The absence of standardized quality management instills apprehension in customers regarding any alterations made to the production process.
- The presence of these quality management issues poses challenges to the customer's sales.
- The factory was unable to fully comprehend the customer's confusion, thus inviting Inertia China to collaborate in resolving these issues.
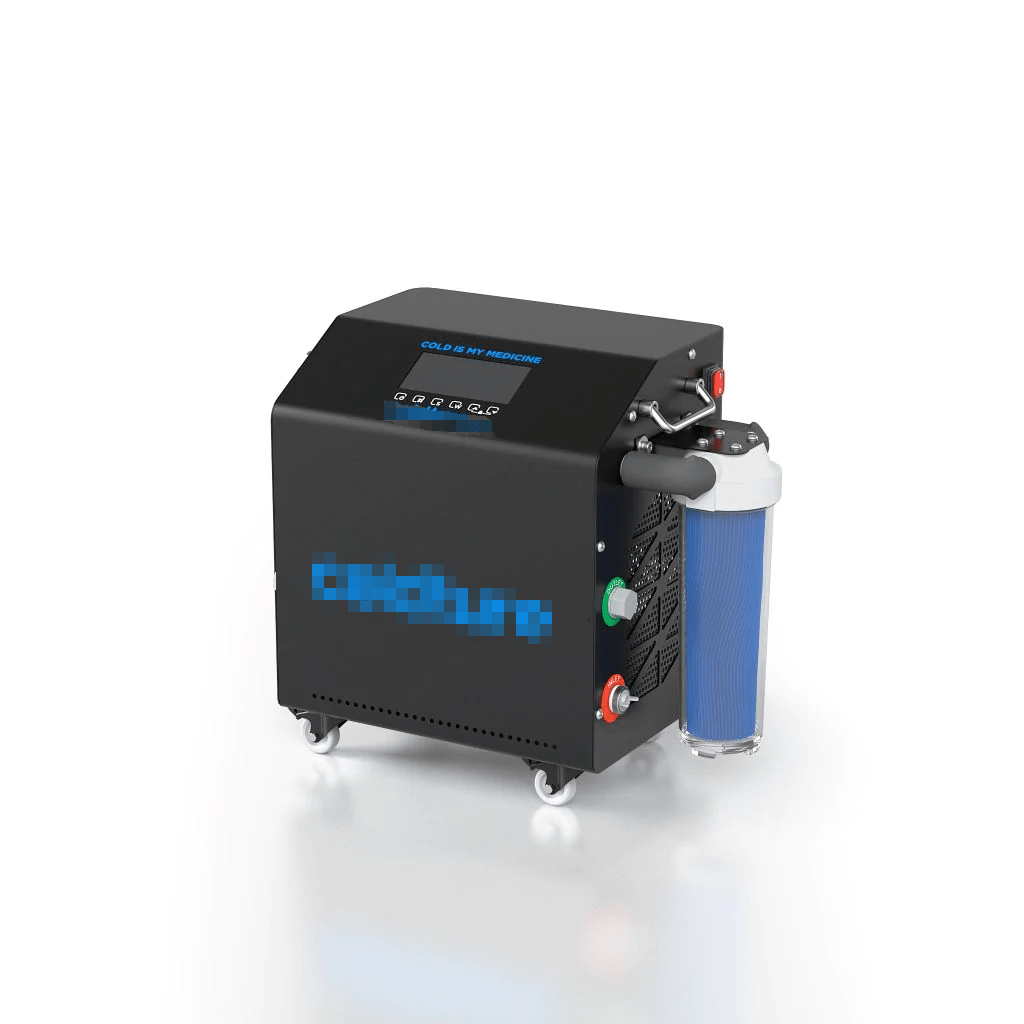
Why Conduct Quality Management
- Does the process flow meet standard quality requirements ?
- Does the products meet your quality requirements?
- Are there any unannounced engineering changes?
- Are there any after-sales troubles caused by products quality management issues
- Does the product …?
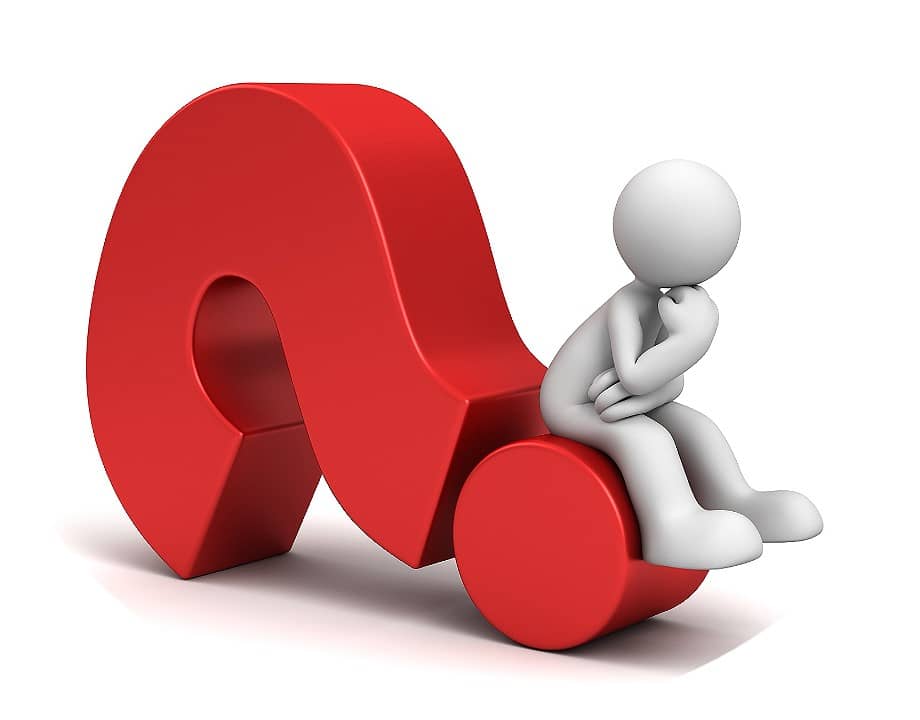
How We Proceed Quality Management?
Step 1 - Launch | Step 2 - On-Site Working | Step 3 - Report | Step 4 - Close |
Work Order
Service Contract Quotation Sales Order Kick-Off |
On-Site Inspection
Daily Quality Report Daily Progress Report Supplier Communication |
Quality Issues Review
DInspection Report Payment Meeting |
Solutions-Suggestion
Continues improvements Lessons Sharing |
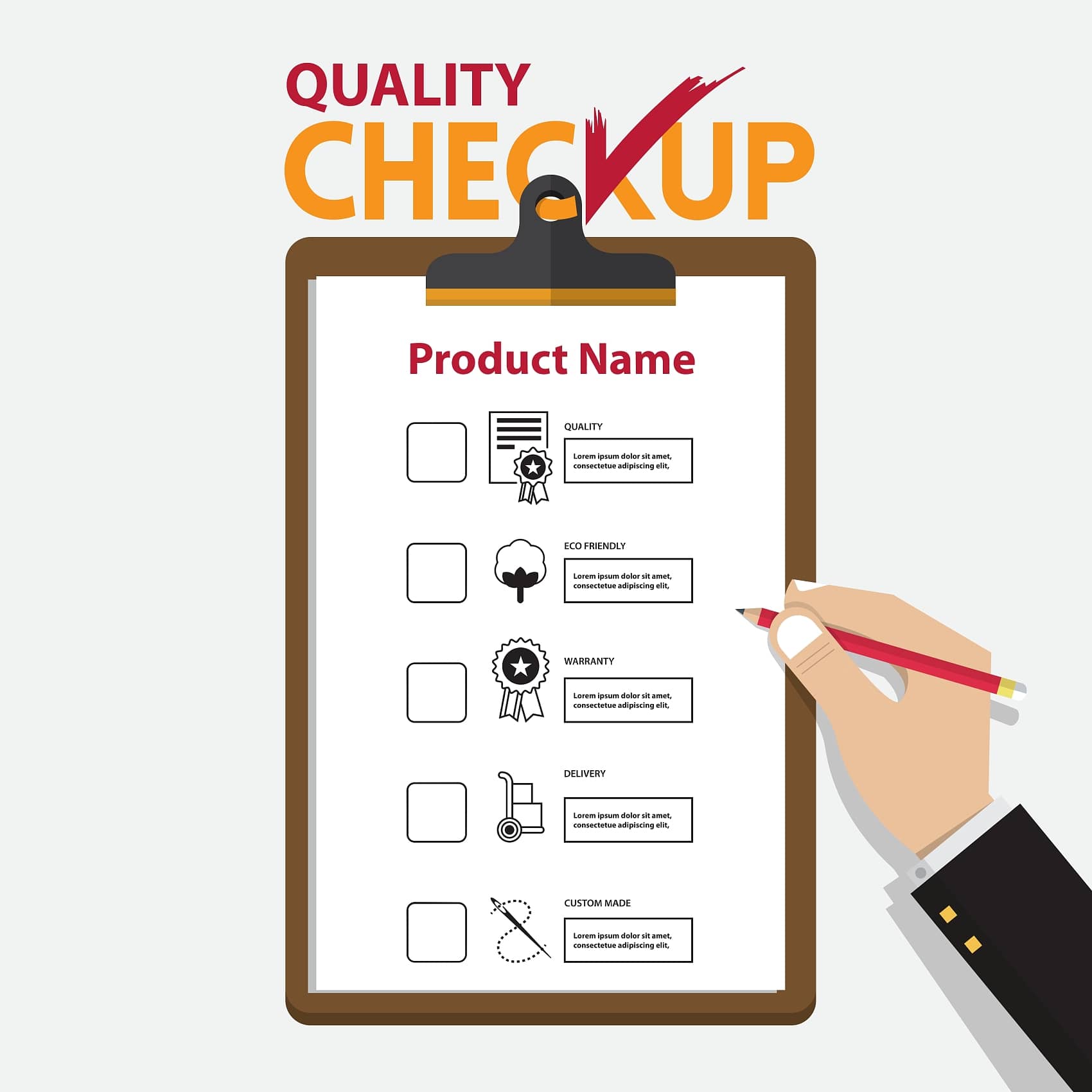
Case Summary
Client’s Quality Concerns
- The customer relinquishes authority over the product's quality level.
- The absence of standardized quality management instills apprehension in customers regarding any alterations made to the production process.
- The presence of these quality management issues poses challenges to the customer's sales.
- The factory was unable to fully comprehend the customer's confusion, thus inviting Inertia China to collaborate in resolving these issues.
Factory Situation
- Factory indeed run some basic quality management but can’t match the client’s requirements.
- Factory indeed has part of QMS system , but it’s not complete cause some quality issues.
Inertia China Quality Management
- Inertia-China check and organize all historical quality issues and report.
- Inertia-China help define some quality standards ( CP\SIP . Etc. ) , which agree with client and factory.
- Inertia-China conduct on-site quality inspection and report , and give some suggestions (solutions or continue improvements).
Quality Results
- Inertia-China helped client understood the actual situation that occurred at factory , then helped factory understood the client’s real concerns.
- Inertia-China also indeed helped factory improve the quality management.
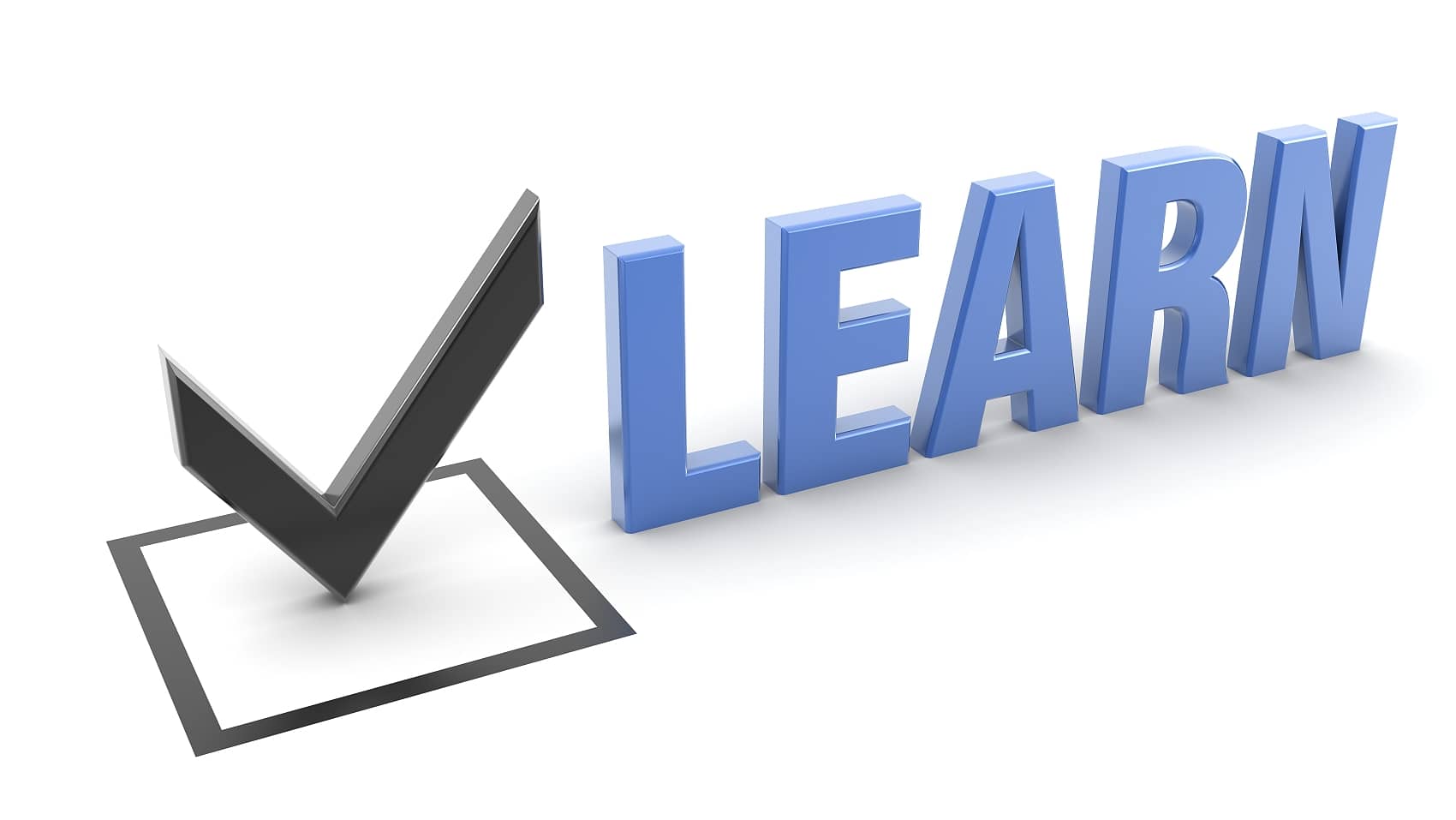